Building Better Batteries
by Alan S. Brown
Lynden Archer changes lithium-ion batteries for the better
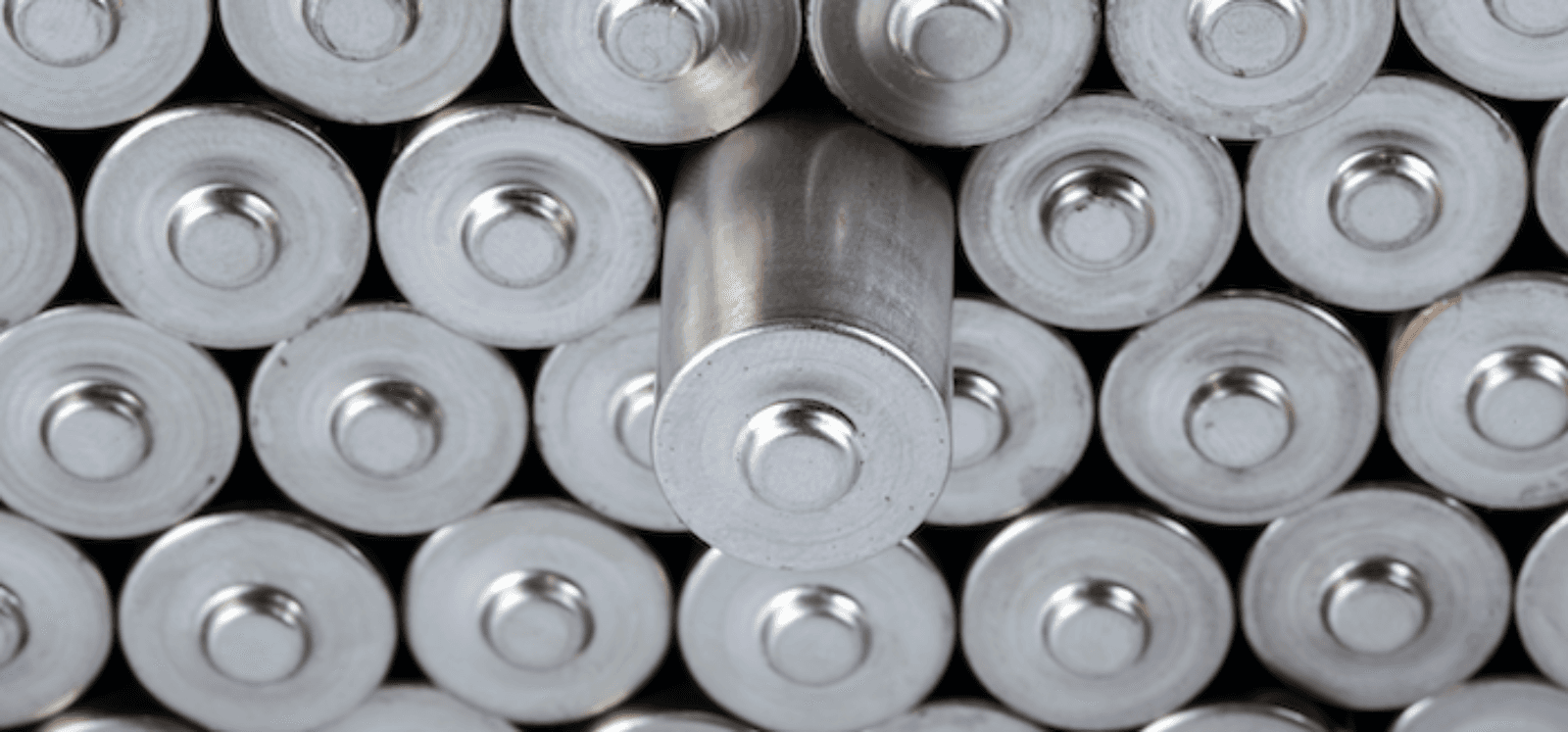
The Author
The Researcher
Portable devices are everywhere, but only because a revolution in lithium-ion batteries makes them possible. Today’s powerful, long-lasting lithium-ion batteries drive everything from smartphones, headphones, and tablets to electric cars, drones, and prosthetics.
The batteries are based on lithium ions, derived from a metal light enough to float on water. They carry more electrical charge for their weight than any other metal.
Yet lithium is unstable. Too much voltage, too high a temperature, and lithium-ion batteries will burst into flames. This has led several giant telecom companies to recall millions of smartphones and, more recently, for airlines to ban lithium-ion batteries in checked luggage.

Lynden Archer, dean of Cornell University’s College of Engineering, and a member of the Kavli Institute at Cornell for Nanoscale Science, has been trying to tame lithium-ion batteries for nearly two decades. Now, by manipulating chemicals at the nanoscale, he is close to a commercial solution.
It is a path that started with his mother’s chickens when he was eight years old.
School
Archer grew up in Guyana, an English-speaking country on the North Atlantic coast of South America. His father, a police inspector, prosecuted cases in court like a lawyer. His mother ran several small businesses, including raising chickens.
“When I was eight years old or so, I read a book that extolled the effect of brewer’s yeast on the metabolism of any animal,” Archer recalled. “The conclusions were so stark, I just had to try it. So my mother bought some brewer’s yeast and gave me some chickens to test and, remarkably, the book’s claims were true. The chickens were healthier and more active.”
Those chickens hooked Archer on science. “It was about reading something, getting wowed about it, and evaluating it,” he said. “That’s where it started for me.”
They also taught him another important lesson: economics matter. While brewer’s yeast made better chickens, it proved too expensive to use on such a small operation.
Like his older brothers, Archer passed a national test at 11 to study science at a prestigious high school. He also took time for sports, playing cricket and ping pong and competing in shot put. “I wasn’t that big, but no one was,” he said. “When I came to America and saw the shot putters, they were so big, I thought they were weightlifters.”
He got to America by a combination of hard work and chance. In high school, he hoped to win a government or corporate scholarship to study abroad. Then an elder brother intervened. He lived in Los Angeles and urged Archer to apply to University of Southern California. That year, USC launched its first International Merit Scholarship and Archer became one of its first two recipients.
Archer dived right in. He studied chemical engineering, a practical discipline that combined his favorites subjects: chemistry, physics, and math. While engineering and science students often form their own community, Archer took a part-time job in a local bookstore and made friends with many liberal arts students.
It was an eye-opening experience that exposed Archer to very bright people studying entirely different but equally rigorous disciplines. “Even today,” he said, “I encourage my son, who is an engineer, to get out of the engineering college and hang out with the artists and scientists. They see the world differently, and their viewpoint is just as valid and important.”
Hybrids
At school, Archer worked in a research lab to develop catalysts to turn the hydrochloric acid emitted by combustion—the cause of acid rain—into industrially useful chorine. To fully test the concept, he helped transform a laboratory process into a larger pilot plant. This hands-on experience inspired him to go to Stanford University to study catalysis as a graduate student.
When he got there, the professor he planned to work with retired. After a “mad scramble” to find a new advisor, he found himself designing laser optical experiments to evaluate models of polymer behavior. His work led to a post-graduate position at AT&T Bell Labs, where he spent a year looking for better ways to make optical fibers.
Because they are made of silica glass, optical fibers crack easily. Researchers believed that if they could mix nanosized silica particles with flexible polymers, they could create a gel that was easier to draw into fibers at the early stages of production. Then they could remove the polymer and leave the desired glass fiber. But when they tried to dry the gel, the silica particles separated from the polymers and left behind a lumpy material that did not transmit light well.
Archer thought he could keep the mixture homogeneous by linking short nanoscale polymer fragments, called oligomers, to the nanoscale silica particles. The result looked something like a nanoscale star with silica in the center and oligomers sticking out. When the oligomers branches bonded with one another, they locked the silica into place.
This work would eventually lead to his battery innovations, but it took years. After his year at Bell Labs, Archer joined the chemical engineering faculty at Texas A&M University. He was still working on ways to make homogeneous nanoparticle-oligomer materials when he moved to Cornell in 2000. Two years later, a conversation with Emmanuel Giannelis led him to batteries.
Electrolytes
Giannelis, currently Cornell’s vice provost for research, earned his reputation by developing nanomaterials for energy and sustainability. When he looked at Archer’s work with silica and polyethylene oxide oligomers, he realized that the chemistry could solve a long-standing problem with lithium-ion batteries.
To understand why, consider how lithium-ion batteries work. They consist of two electrical conductors, called electrodes, with an electrolyte between them. Lithium atoms give up electrons to create electricity when they discharge. This turns them into positively charged ions, which move through the electrolyte to the negative electrode, where they are recharged with new electrons.
Researchers believed polyethylene oxide would make an outstanding electrolyte for three reasons: First, it helps free lithium ions so they can leave the electrode. Second, they offer very little electrical resistance to moving ions. Third, compared with commercial lithium-ion electrolytes, polyethylene oxide is less volatile and poses less risk of fire.
Yet polyethylene oxide has one great flaw—it crystallizes at 60 C (140 F). Ions can scarcely move through its solid body, so polyethylene oxide-based batteries will not work at room temperature.
Archer understood how to circumvent this problem: “We were working at the nanoscale, using very short, lightweight polyethylene oxide oligomers bound to nanoscale particles of silica,” he said. “At the nanoscale, the smaller the tethered oligomer, the more agitated it is anchored to a nanostructure, which lowers its melting point. So if we make those oligomers small enough, they will remain amorphous instead of crystallizing at room temperatures. Meanwhile, glassy silica cores improved the electrolyte’s mechanical properties.”
Since the silica was bound to the branched polyethylene oxide oligomers, the concentration of silica and polyethylene oxide in the electrolyte was uniform from one end of the battery to the other, and its conductivity and mechanical properties could be adjusted simply by controlling how much polyethylene oxide bonded to each silica particle.
“It was like having a bucket of silica marbles, and the white space in between them was where the lithium ions were able to move,” Archer said.
The result was a new type of electrolyte that was intrinsically safe and that could potentially handle higher voltages. In 2010, Archer helped found NOHMs Technologies to commercialize the technology. The company spent the past 10 years developing even better electrolytes (based on salts that remain liquid at room temperature) and ratcheting down the cost. It is now poised to bring multiple products to market.
Around the same time Archer founded NOHMs, he became head of Cornell’s School of Chemical and Biomolecular Engineering. In 2017, he was appointed director of the University’s Energy Systems Institute, which focuses on technologies that lower humanity’s carbon footprint, where he emphasized translating “research into products that have impact on people’s lives.”
In June 2020, Cornell’s College of Engineering named Archer dean. Although he is new in the position, he has been focusing on developing strategic priorities, which he defines as “things an influential institution must dream about, even in these uncertain times.”
Part of that involves new investments. “Our engineering college is housed in infrastructure that was designed in the 1950s, when engineering was large and mechanical. Today, it is nano, wet, and biological,” he said.
“One of our challenges is to upgrade that infrastructure so we can position the college to address emerging fields, not just with new buildings, but with the novel engineering science enabled by such facilities. The Kavli Institute at Cornell’s advanced laboratory equipment will play an instrumental part in that.”
It is an ambitious agenda for someone who started his research career as an eight-year old by feeding brewer’s yeast to chickens.