Microbots with Nano-Origami Joints
by Alan S. Brown
A new generation of microscale robots promises to wed semiconductors, solar cells, and sensors with complex 3D origami shapes and functions
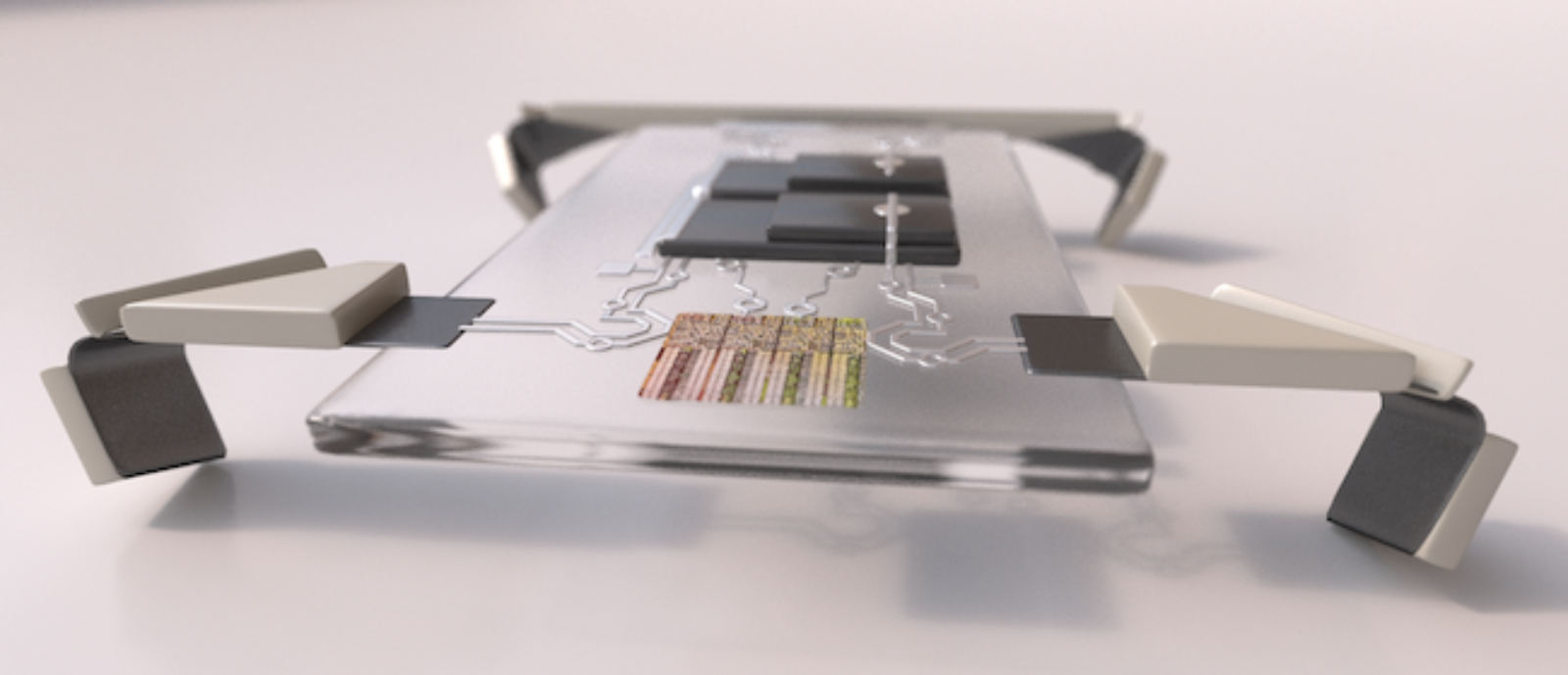
The Author
The Researcher
Under a microscope, Itai Cohen’s microbots come to life.
The four-legged robots are so small, Cohen and his collaborators at the Kavli Institute at Cornell for Nanoscale Science can build one million of them on a single 4-inch silicon wafer. When their legs start beating, they look like an army of water bugs skittering over a pond.

Equally important, these microbots are made from silicon wafers the same way industry makes computer processors, solar cells, and sensors. Although semiconductor devices are flat, Cohen and his fellow researchers are using the ancient Japanese arts of origami (folding) and kirigami (cutting) to turn nanometer-thin slivers of silicon into three-dimensional robots.
Since nanoscience’s earliest days, visionaries like Eric Drexler, in his book, Engines of Creation, have promised nanoscale machines that could do things like attack tumors, build precision instruments, and—to pick something mundane but useful—unclog drains. Until now, that promise has remained unfulfilled.
Cohen’s microbots, however, may be the first step on the road to truly smart microscale—and one day, nanoscale—machines.
Physics at the edge
The seeds for Cohen’s eccentric approach were planted as a graduate student at the University of Chicago, when he attended a lecture by Sidney Nagel on singularities, cases where the mathematical rules describing an object’s behavior break down. While most physicists apply the term to black holes, Nagle showed that the same mathematics describe a drop of water as it drips from a faucet.
“It was fascinating,” Cohen said. “I could study these extreme phenomena on a benchtop without a black hole sucking up the whole lab.”
Studying singularities in everyday phenomena taught Cohen to work creatively by “borrowing and stealing” insights from other fields. It was his passion for studying subjects on the periphery of physics that led him to origami and robots at Cornell.
Cohen came to origami through a grant that allowed him to study the mechanical properties of origami structures and their transformations. He probed the mathematics of how valley-like structures could snap instantly into mountain-like objects and totally change an object’s mechanical behavior.
Meanwhile, his colleague, Paul McEuen, the Kavli Institute’s co-director, was exploring kirigami, an origami variant that uses cuts as well as folds. McEuen worked with graphene, a form of carbon only a few atoms thick. He reasoned that kirigami would enable him to turn graphene into three-dimensional nanoscale objects.
“We started dreaming,” Cohen said. “And that got us thinking about how to make machines at the nanoscale.”
Origami robots
From the start, they wanted to use semiconductor technology so they could combine computer chips with mechanical parts.
“What we wanted was two-dimensional circuits that could fold themselves up into a machine and go off to do something,” Cohen said.
Together with Marc Miskin (now at University of Pennsylvania), a post-doctoral researcher they hired to combine the expertise of their labs, they developed a folding technology to make nanobot legs.
They started with a silicon body and four folded legs made of thin platinum strips coated on one side with titanium. As a solar cell charged up the platinum, it attracted ions floating nearby. These absorbed onto the platinum surface and caused it to contract while the titanium layer remained unaffected. This pulled the titanium around the platinum, bending it like a knee.
To create actual joints, the researchers coated some of the platinum with small plastic pads. The leg folded—at blinding speed—only where the platinum was exposed.
The first microbot legs folded only in one direction. A graduate student in Cohen’s lab, Baris Bircan, developed a way to fabricate nanoscale films with mountain and valley folds that bend in either direction. This allowed the group to create the world’s smallest folded bird and structures with upwards of 100 folds. Other lab members are now using these methods to make more sophisticated robots.

“The ability to cut and fold in either direction means that all origami and kirigami strategies are now open to us,” Cohen said.
For Cohen, this is just the start. He is already imagining possible applications, from beating arrays of robotic “legs” to pump and mix fluids in lab-on-a-chip diagnostics to microbots that change their shape to encapsulate and kill tumors.
Most of all, though, he envisions truly smart microbots. Cornell’s nanofabrication facility, he explained, could design a processor to fit on a microbot.
“That means you can put the computational power of the spaceship Voyager on a machine that is smaller than the width of a human hair,” he said. “And that is fantastic."